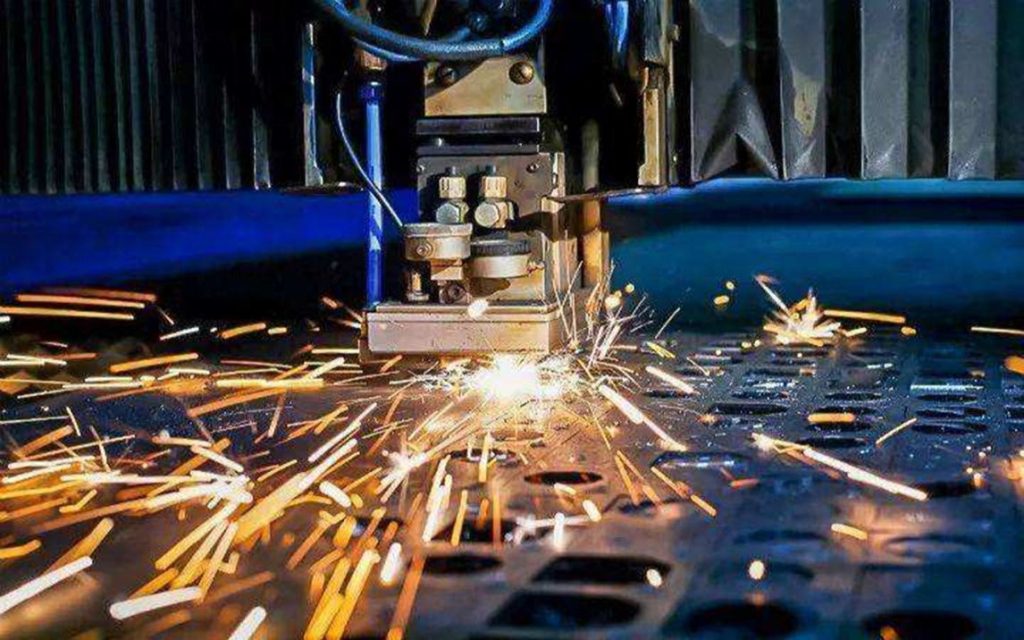
Surface treatment of metals is a surface protection technology that enhances the corrosion resistance and wear resistance of products by altering the mechanical, physical, and chemical properties of the substrate material’s surface.
Traditional surface treatment methods mainly include electroplating, electrophoresis, blackening, bluing, phosphating, passivation, spraying, coloring, infiltration, baking paint, sandblasting, brushing, polishing, and anodizing.
Electroplating
What is electroplating?
Electroplating is the process of depositing a layer of another metal or alloy on the surface of certain metals using the principle of electrolysis.
Classification of electroplating
According to the composition of the coating, electroplating processes can be categorized into zinc plating, chromium plating, tin plating, copper plating, nickel plating, cadmium plating, gold plating, silver plating, etc.
Galvanizing
Zinc is easily soluble in acid and also in alkali, hence it is called an amphoteric metal. Zinc hardly changes dry air. It is mainly used to prevent corrosion of steel, and the effectiveness of its protective properties is closely related to the thickness of the coating.
Chrome Plating
Chrome is a silver-white metal with a faint bluish tint. It possesses strong passivation properties, quickly passivating in the atmosphere, exhibiting the characteristics of a noble metal. Therefore, chrome plating on iron components is cathodic plating. Chrome coatings have high hardness, good wear resistance, strong reflectivity, and excellent heat resistance.
Tin Plating
Tin has a silver-white appearance and offers advantages such as corrosion resistance, non-toxicity, ease of soldering, and good ductility. Tin coatings exhibit high chemical stability.
Copper Plating
Copper coatings appear pink, have a soft texture, and possess good ductility, electrical conductivity, and thermal conductivity. They are easy to polish. Through appropriate chemical treatments, various decorative colors such as antique bronze, copper green, black, and natural color can be achieved.
Cadmium Plating
Cadmium is a shiny, soft silver-white metal. It is harder than tin but softer than zinc, with good malleability, making it easy to forge and roll. Chemically, cadmium is similar to zinc, but it does not dissolve in alkalis. It is soluble in nitric acid and ammonium nitrate, and dissolves slowly in dilute sulfuric acid and dilute hydrochloric acid. Cadmium vapor and soluble cadmium salts are toxic, requiring strict prevention of cadmium contamination. Due to the significant hazards of cadmium pollution and high cost of Cadmium, zinc plating or gold plating is commonly used instead of cadmium plating.
Gold Plating
Electroplated gold coatings exhibit strong corrosion resistance, good conductivity, ease of welding, high-temperature resistance, and a certain degree of wear resistance. They also possess excellent resistance to color change. Additionally, gold alloy plating offers various shades, and gold plating on silver prevents discoloration. However, due to the high cost of gold, its application is subject to certain limitations.
Silver Plating
This plating is utilized to prevent corrosion, enhance conductivity, improve reflectivity, and enhance aesthetics. It finds extensive application in the manufacturing industry for electrical appliances, instruments, meters, and lighting fixtures.
Electrophoresis
What is electrophoresis?
Electrophoresis is a process where pigments, resins, and other substances are suspended in a liquid, and under the action of a direct current field, charged particles move in the electric field, eventually depositing on the electrode surface to form a uniform, dense, and smooth film layer.
The advantages of electrophoretic coating include fast film formation, uniform coating, good corrosion resistance, and good wear resistance, making it suitable for surface coatings of parts that require certain decorative and anti-corrosive properties.
Difference between electroplating and electrophoresis
The difference between electroplating and electrophoresis lies in the intermediary substances involved. In electroplating, metal ions are utilized, whereas electrophoresis employs colloids.
The resulting outcomes also differ. Electroplating deposits a layer of metal, providing protection, corrosion resistance, and aesthetic functions, while electrophoresis is typically used for painting surfaces, commonly in the automotive industry.
Electroplating has a metallic texture. Electrophoresis is merely a high imitation of electroplating, with some performance and color differences. It’s challenging for electrophoresis to achieve the metallic texture of electroplating.
Blackening and Bluing
What are blackening and bluing?
Blackening and bluing are common surface treatments in the industrial manufacturing sector, aimed at improving the rust and corrosion resistance of steel structural components while enhancing aesthetics.
Difference between blackening and bluing
The processes for blackening and bluing are entirely identical in terms of technique; the difference lies solely in the contrasting outcomes caused by variations in temperature.
At a high temperature of 550℃, ferric oxide will exhibit a sky-blue color, hence referred to as “bluing treatment”. However, at a lower temperature of 350℃, ferric oxide will appear black, thus termed as “blackening treatment”.
In many cases, surface blackening treatment of components is also referred to as bluing treatment.
Phosphating and Passivation
What are phosphating and passivation?
Phosphating and passivation are both pre-treatment processes for metal coating.
Phosphating is a process where a chemical and electrochemical reaction forms a phosphate conversion coating, known as a phosphate film. Phosphating is a commonly used pretreatment technique. On one hand, it protects the substrate metal, to some extent preventing corrosion. It is used as an undercoat before electrophoresis to enhance paint adhesion and corrosion resistance. On the other hand, the porous nature of the phosphate film allows coatings to penetrate into these pores, tightly bonding with the phosphate film, thus improving paint adhesion. Phosphating treatment is generally applied to the surface of steel and iron components.
Passivation refers to the process where metals undergo oxidation treatment using strong oxidizing agents or electrochemical methods, resulting in the surface becoming less reactive. It transforms the metal surface into a state less susceptible to oxidation, thus slowing down the metal’s corrosion rate. Passivation acts as a complete barrier between the metal and the corrosive medium (simply put, it prevents rust). It is commonly applied to workpieces prone to oxidation reactions with air, such as zinc alloys and electroplated parts.
Spraying and Coloring
What are spraying and coloring?
Coloring refers to a chemical reaction occurring on the surface of a component under certain conditions, where the elements of the component itself react, such as aluminum oxidation forming various colors. Spraying is the process of applying another substance onto the surface of a component, such as spray painting or plastic powder spraying.
Spray painting
Spray painting refers to a processing method where paint is atomized through a spray gun and applied to the surface of an object. There are various methods including compressed air spray painting, high-pressure airless spray painting.
Powder spraying
Powder spray is a surface treatment where plastic powder is sprayed onto parts. The working principle involves charging the plastic powder through high-voltage electrostatic equipment, and under the influence of the electric field, the coating is sprayed onto the surface of the workpiece. The powder is evenly adsorbed onto the surface, forming a powdered coating. After high-temperature baking, the powdered coating melts and solidifies, creating a dense protective layer with different effects, firmly adhering to the surface of the workpiece.
Infiltration
What is infiltration?
Infiltration is a microporous sealing process, providing a permanent solution for the pores in castings. Sealants are infiltrated through natural penetration, vacuum suction, or pressurization to fill gaps. Its main purpose is to achieve sealing of gaps.
Scope of infiltration process: Engine cylinder blocks, cylinder heads, housings, hubs, shells, valves (water, gas, oil), water pumps, etc.
Baking Paint
What is baking paint?
Baking paint involves applying three coats of primer and four coats of finish paint on the substrate, with each coat being baked in a dust-free constant-temperature baking room.
Characteristics of baking paint
Non-stickiness
Virtually all substances do not adhere to the PTFE coating, even thin films exhibit excellent non-stick properties.
Heat resistance
PTFE coatings have excellent heat and low-temperature resistance characteristics. They can withstand temperatures up to 300℃ for short periods and can be used continuously between 240℃ and 260℃, showing remarkable thermal stability.
Slipperiness
PTFE coatings have a low coefficient of friction. The coefficient of friction changes slightly under load sliding but remains between 0.05 and 0.15.
Resistance to moisture
The surface of PTFE coatings repels water and oil, making them resistant to solutions during production operations. If contaminated, they can be easily cleaned by simple wiping.
Wear resistance
Baking paint exhibits excellent wear resistance under high loads, providing both wear resistance and non-adhesiveness under certain loads.
Corrosion resistance
PTFE coating exhibits excellent corrosion resistance, effectively resisting chemical corrosion from acids, alkalis, salts, and other substances.
Shot Blasting and Sandblasting
What is shot blasting and sandblasting?
Shot blasting uses compressed air as power to propel steel shot onto the surface of the workpiece, cleaning or strengthening the surface in the process.
Sandblasting, similar to shot blasting, uses compressed air as power to propel abrasive materials (such as copper ore sand, quartz sand, emery, and iron sand) onto the surface of the workpiece for surface treatment.
Difference between shot blasting and sandblasting
Both shot blasting and sandblasting use high-pressure air or compressed air as power to clean the workpiece surface, but the choice of media and the effects differ.
After sandblasting, contaminants on the workpiece surface are removed, and the surface is slightly damaged, increasing the surface area significantly. As a result, the adhesion strength between the workpiece and the coating/plating is increased. The surface of the workpiece after sandblasting is in its natural color but lacks metallic luster due to the rough surface, resulting in a matte finish.
After shot blasting, contaminants on the workpiece surface are removed without significant damage to the surface. The surface area of the workpiece increases slightly. During processing, excess energy generated will strengthen the surface of the workpiece. The surface of the workpiece after shot blasting is in its natural color, but due to the spherical surface, some light is refracted, resulting in a semi-gloss effect.
Brushed Finish
What is brushing?
Brushing is the process of forming different types of fine filigree marks on the surface of metal by abrasive materials under pressure. This primarily involves physical mechanical friction processes, sometimes accompanied by chemical corrosion procedures, creating a thread-like texture on the metal surface. Brushed finish can be made into various patterns according to decorative needs, such as straight, irregular, corrugated, and spiral hairline.
Polishing
What is polishing?
Polishing is a finishing process for refining the surface of parts, typically resulting in a smooth surface without improving or maintaining the original machining accuracy. The Ra value after polishing varies from 1.6 to 0.008um depending on the pre-processing conditions. It is generally divided into mechanical polishing and chemical polishing.
Anodizing
What is anodizing?
It mainly refers to the anodizing of aluminum and aluminum alloys. Anodizing is the process of immersing aluminum or aluminum alloy parts in the acidic electrolyte solution and applying an external current as an anode to form a corrosion-resistant oxide film firmly bonded to the substrate surface. This oxide film has special properties such as corrosion resistance, decoration, insulation, and wear resistance.